Produzione di resine
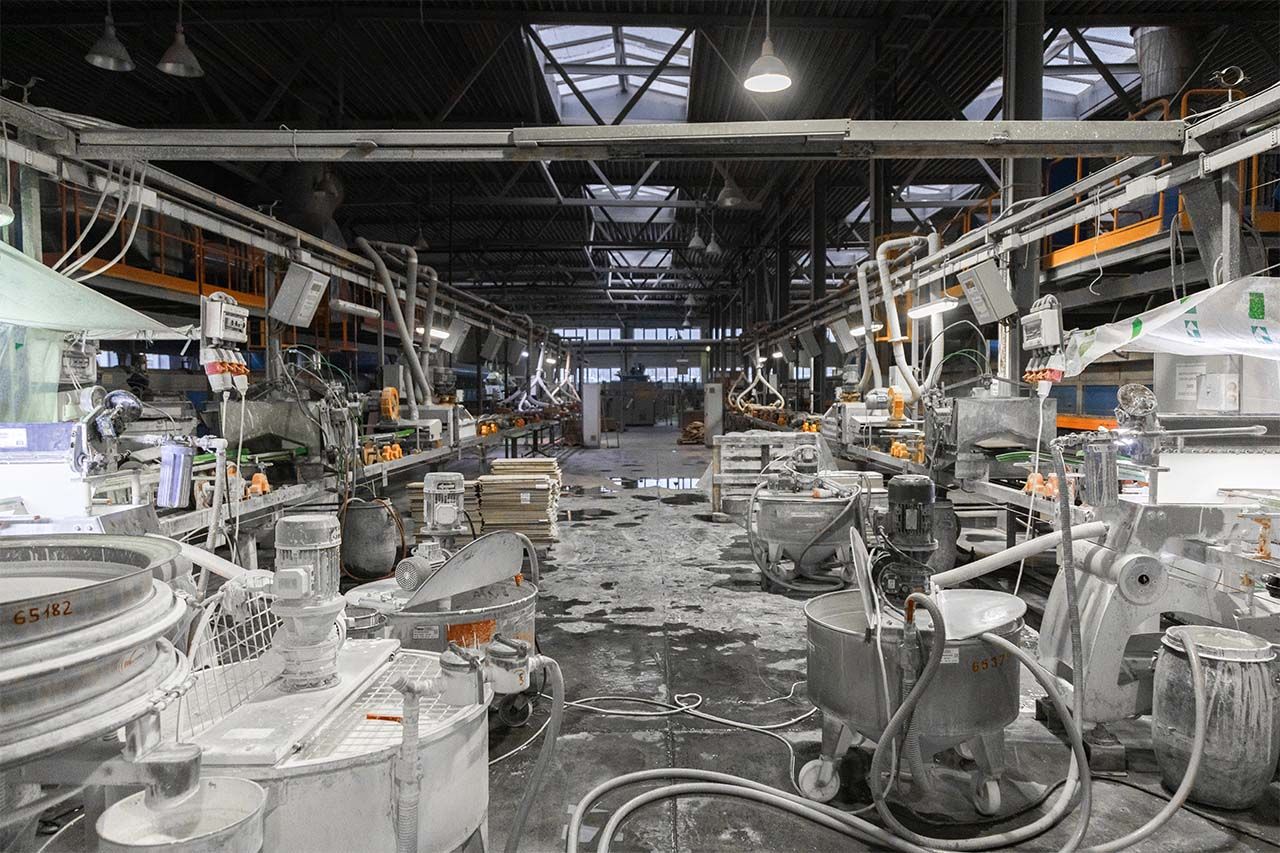
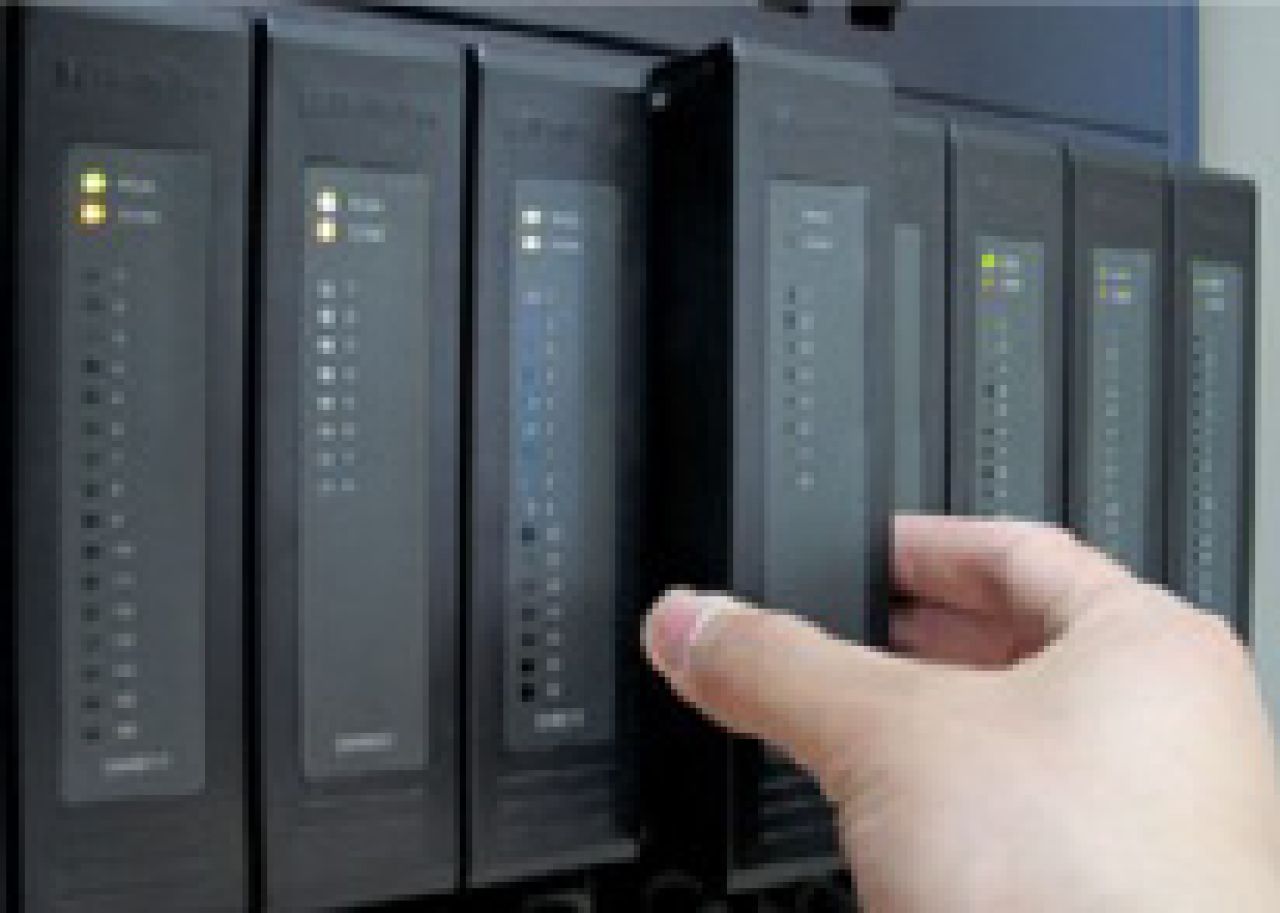
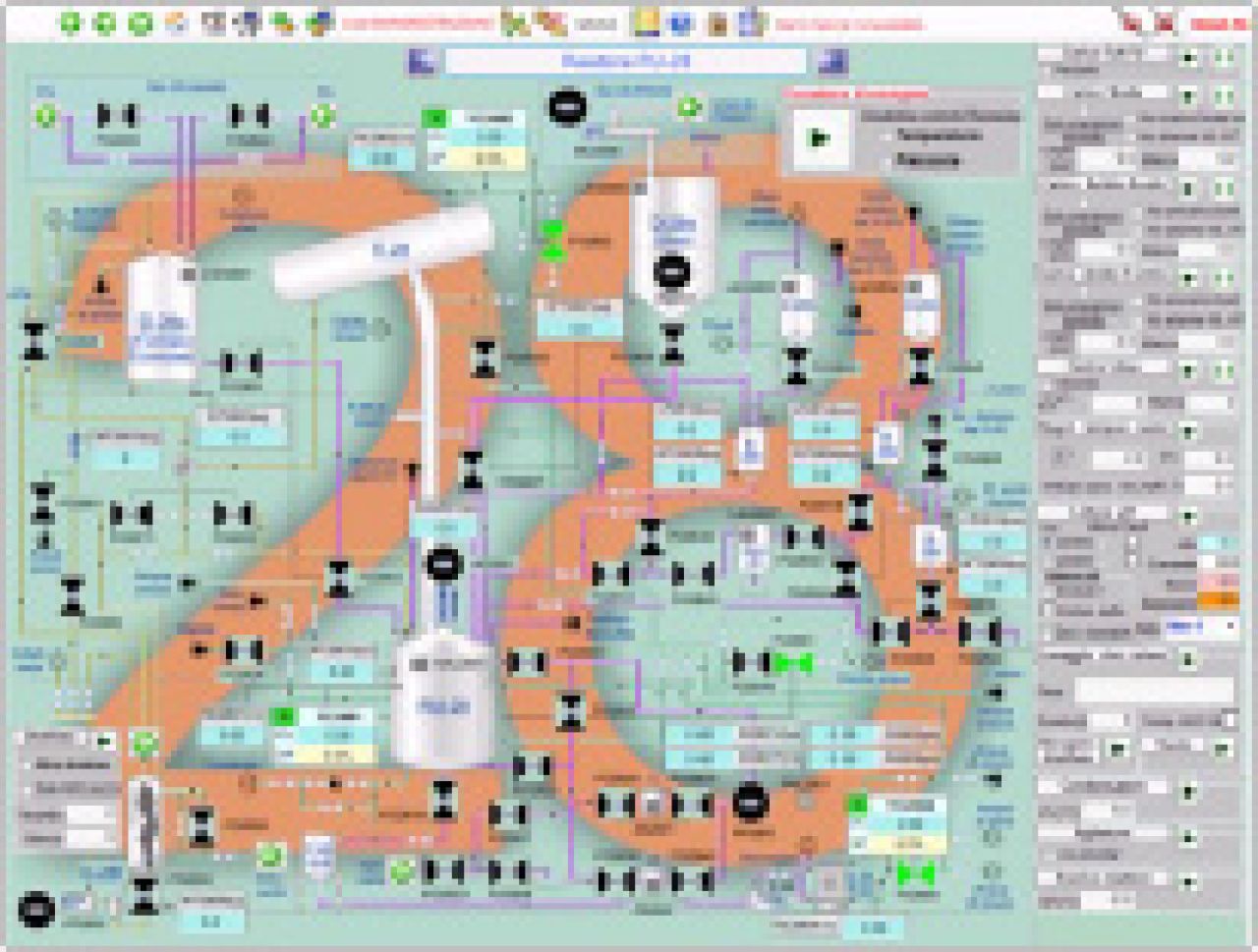
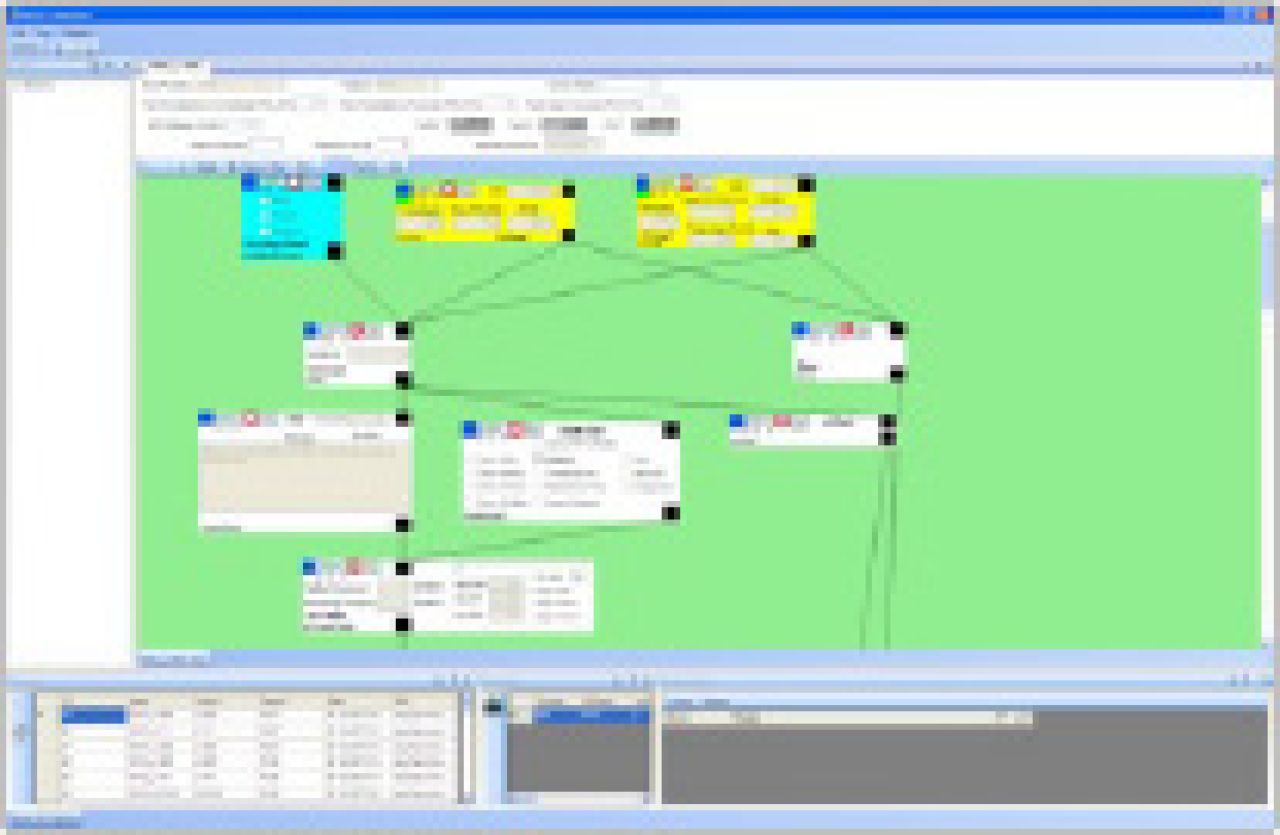
Il cliente
Il cliente, situato nella zona di Bergamo, è un grosso produttore di resine di diversa tipologia (acriliche, viniliche, ureiche, fenoliche). C.Si.Co. ha realizzato l’automazione di tutti i reparti; qui viene presentato il solo caso del reparto resine ureiche.
Il progetto
Un impianto esistente, costituito da reattori di diverse taglie (da 5 a 30 ton), produce resine ureiche. La conduzione dell’impianto è manuale, e il cliente intende installare un sistema di automazione al fine di:
- diminuire l’incidenza di errori operativi,
- incrementare la produttività, riducendo i tempi morti e l’influenza del fattore umano,
- migliorare la qualità, diminuendo lo scostamento del prodotto dai requisiti ottimali e minimizzando le differenze tra lotti diversi.
Il processo di produzione delle resine ureiche è esotermico; ciò significa che nella fase critica un guasto del sistema di controllo è potenzialmente in grado di creare danni ai macchinari e all’ambiente. Quindi è richiesto un sistema sicuro.
La soluzione
Il sistema si basa su un controllore di tipo ridondato (DCS). In accordo con il cliente, si decide di utilizzare un prodotto completamente nuovo e sconosciuto in Italia.
Questo DCS è stato individuato dalla ricerca e sviluppo C.Si.Co., e testato nei laboratori prima di proporlo al mercato, come alternativa ai sistemi più conosciuti, che C.Si.Co. ha già estensivamente applicato (Siemens S7H, ABB, MTL, …).
Esso abbina alla sicurezza tipica del DCS, un sistema di programmazione particolarmente efficiente e costi inferiori al 50% rispetto ai prodotti normalmente usati.
Sul piano della interazione da parte degli operatori, C.Si.Co. ha da tempo messo a punto sistemi di supervisione completamente basati su personal computer, permettendo in tal modo di eliminare i costosi pannelli di controllo elettromeccanici.
Oltre ad aver acquisito una notevole esperienza in molti dei software di supervisione presenti sul mercato (iFix, WinCC, Intouch, Movicon, Zenon per citarne solo alcuni) C.Si.Co. ha costruito nel tempo una serie di librerie e driver di supervisione nativi per Windows, consolidandoli in ormai più di 50 installazioni; grazie a questo lavoro, C.Si.Co. realizza applicazioni di supervisione impianti con funzionalità client/server senza la necessità di acquistare licenze di pacchetti specifici, abbattendo così notevolmente i costi fissi.
Il cliente accoglie questa soluzione, raggiungendo in tal modo un abbattimento complessivo di oltre il 70% sui costi fissi del sistema, senza rinunciare a nessuna delle funzionalità richieste, e con un look & feel decisamente accattivante.
Date le esigenze restrittive del cliente, il periodo di messa in servizio deve essere completato nel giro di due settimane, nel periodo di chiusura dei reparti per le ferie estive.
Per soddisfare questa esigenza, C.Si.Co. realizza test estensivi simulati dell’applicazione complessiva, riuscendo così a porre l’impianto in produzione in una sola settimana.
Trattandosi di un processo batch, C.Si.Co. propone successivamente al cliente una gestione automatizzata anche della sequenziazione delle fasi del processo, in grado di incrementare ulteriormente i risultati.
Anche qui, C.Si.Co., grazie agli sviluppi della propria libreria nativa Windows, è in grado di proporre una soluzione MES efficace ma estremamente economica, non dovendo ricorrere a pacchetti commerciali dai notevoli costi di licenza.
Il batch controller si interfaccia al sistema gestionale aziendale, recependo da esso gli ordini di produzione e ritornando i dati produttivi.
Inoltre viene gestita una base dati di materie prime, con messaggistica di avvertimento per il lancio di ordini di approvvigionamento con sufficiente anticipo.
I risultati
Dopo alcuni mesi di produzione ed assestamento, il cliente dichiara che tutti gli obiettivi sono stati raggiunti.
- Dal momento dell’installazione, non si sono più verificati errori operativi, portando quindi il loro numero dalla media precedente di tre al mese allo zero, con un vantaggio economico dovuto alla riduzione delle perdite di diverse decine di migliaia di Euro nei primi sei mesi.
- I tempi morti si sono annullati, poichè è stata eliminata del tutto la variabilità dovuta al fattore umano. Gli operatori assumono ora una funzione di controllo, riducendo drasticamente i tempi di manovra e la fatica.
La produttività dell’impianto è stabile e costante anche nei turni notturni e nei fine settimana.
- Ottimi i risultati anche sul fronte della qualità. Se precedentemente il 13% del prodotto veniva rigettato dal cliente per non conformità di produzione, nei primi sei mesi di esercizio, questa percentuale si è ridotta al 5%.
Si è potuto verificare che questo era dovuto ad una non corretta definizione dei parametri produttivi da parte degli ingegneri di processo, non ad imperfezioni del processo condotto dal sistema.
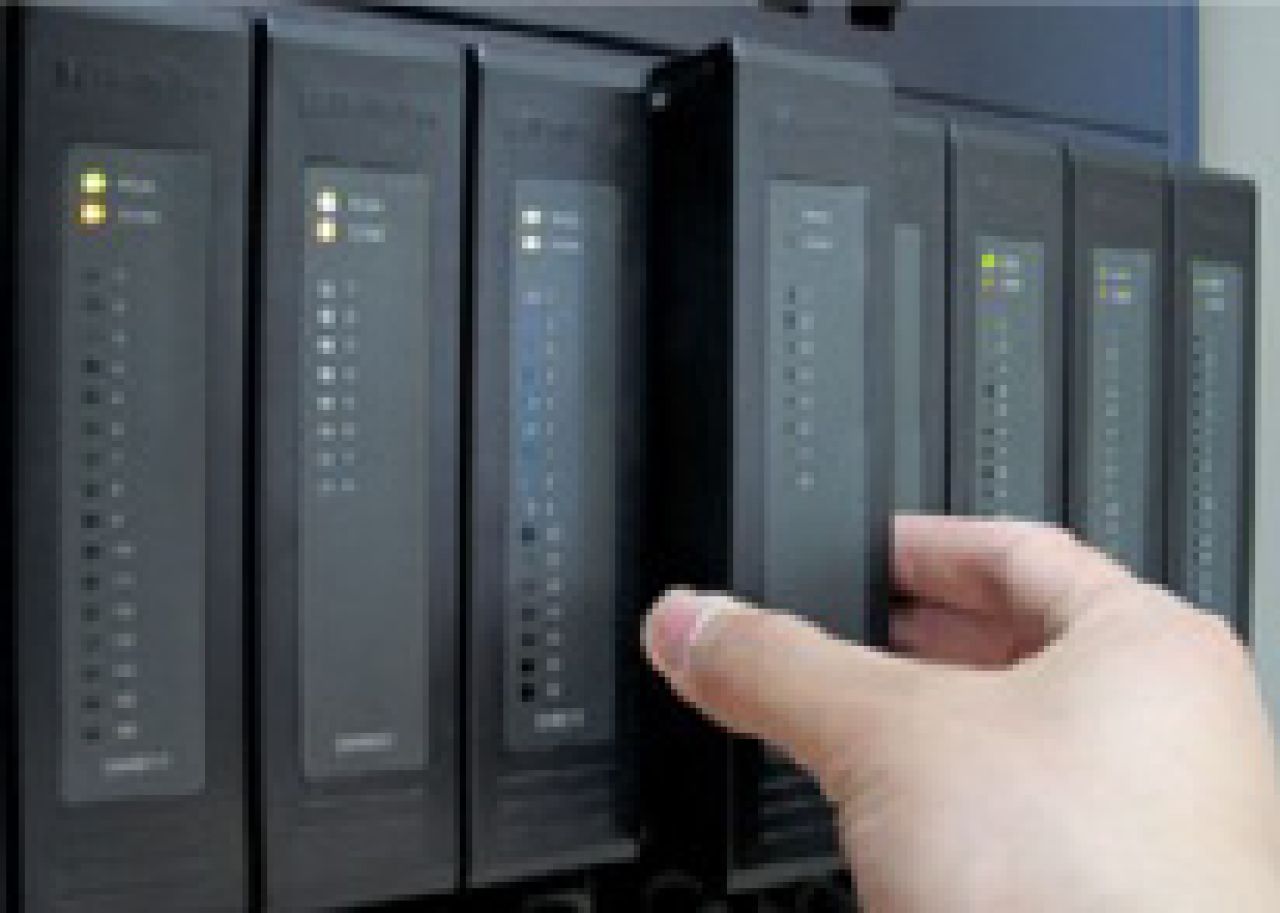
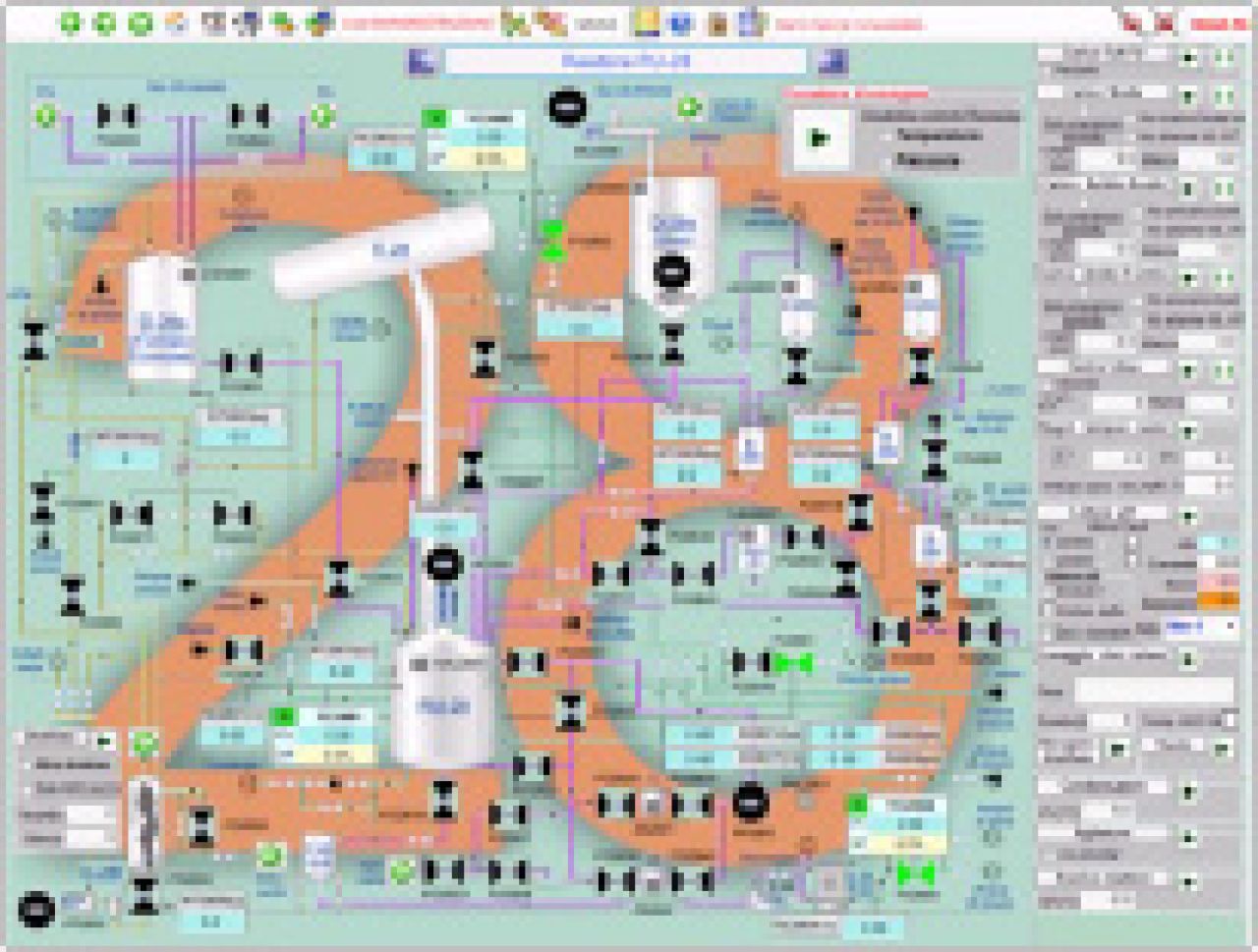
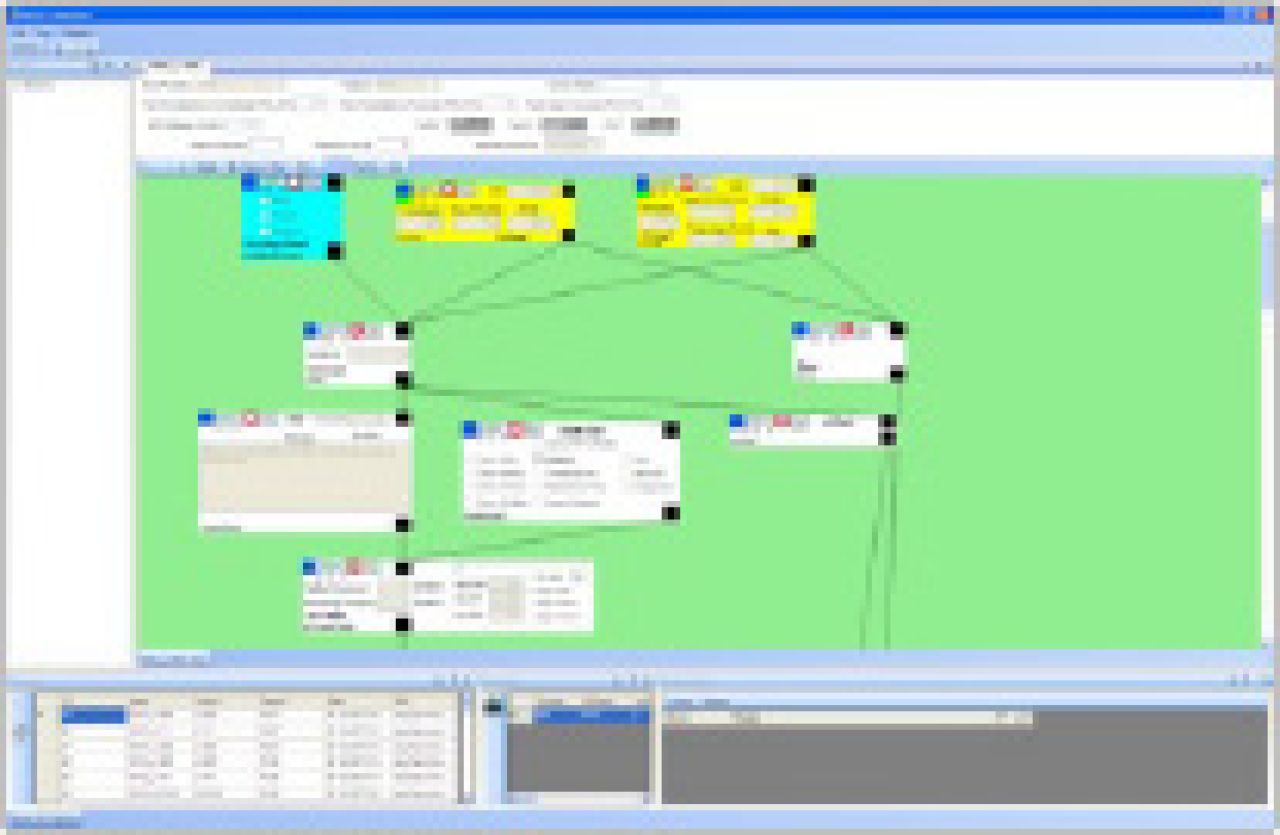