Produzione di Biodisel
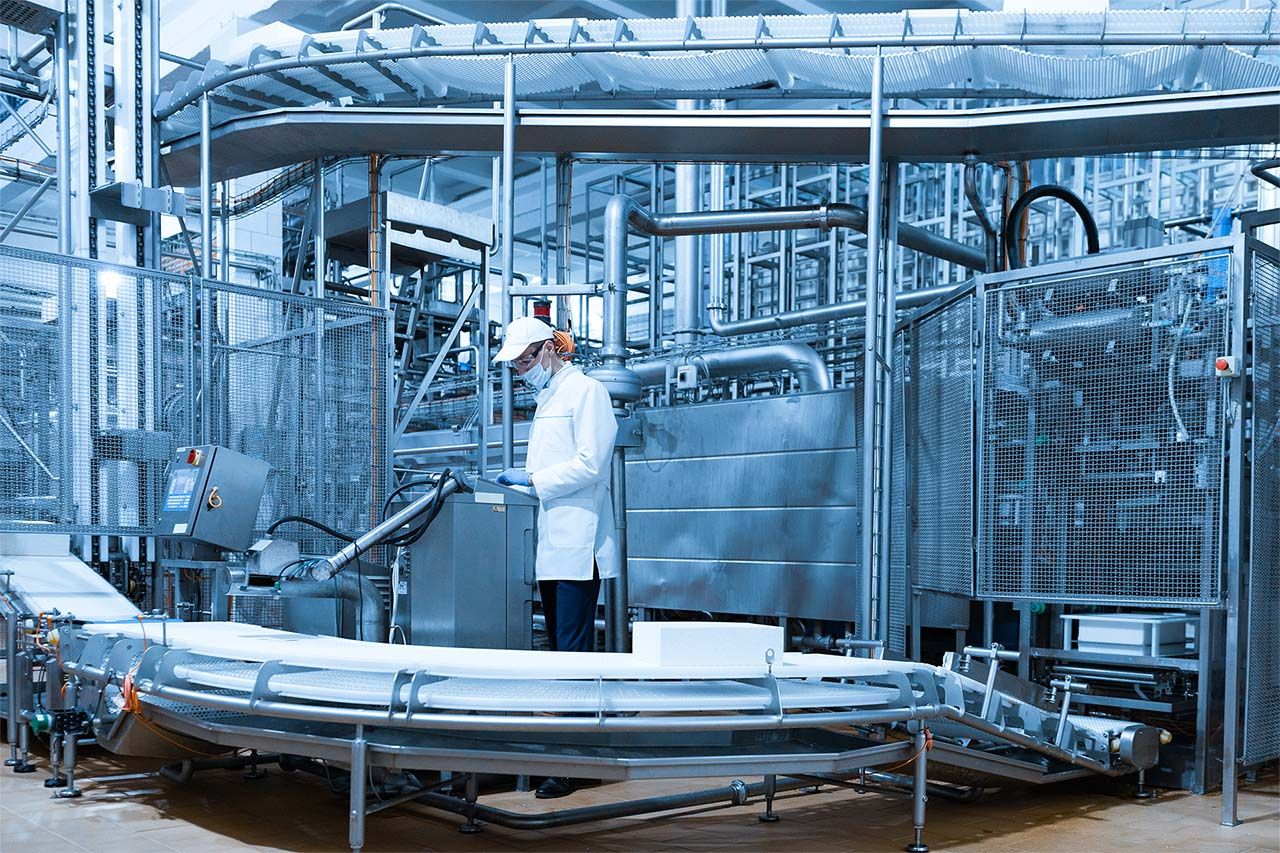
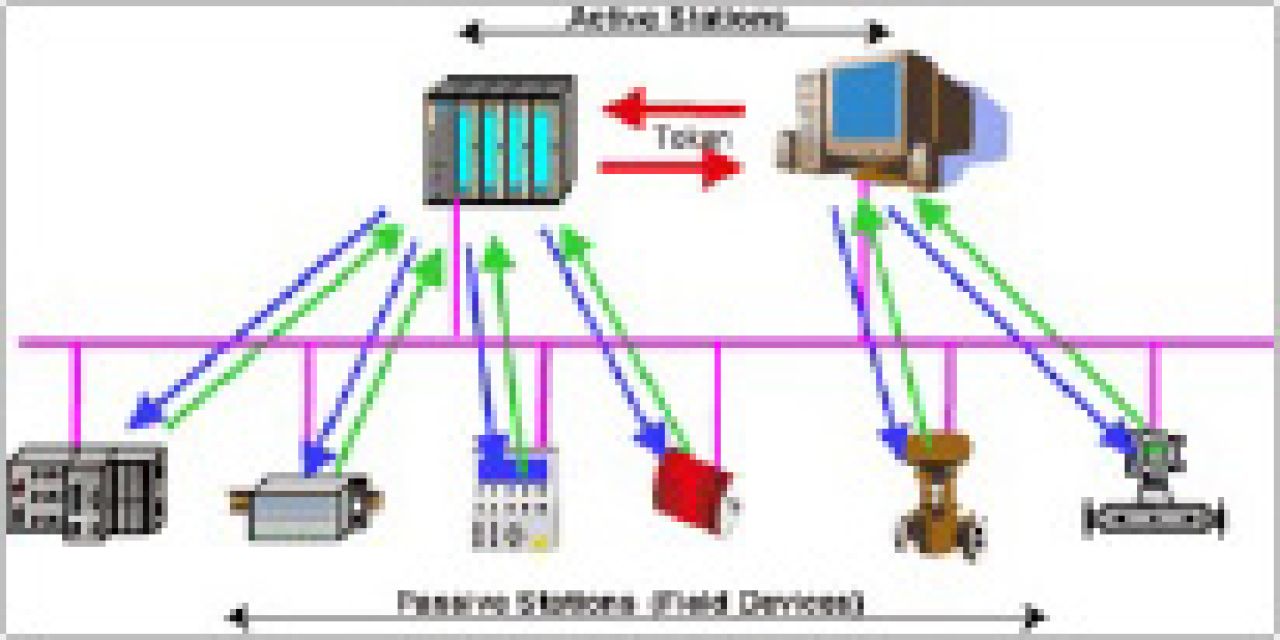
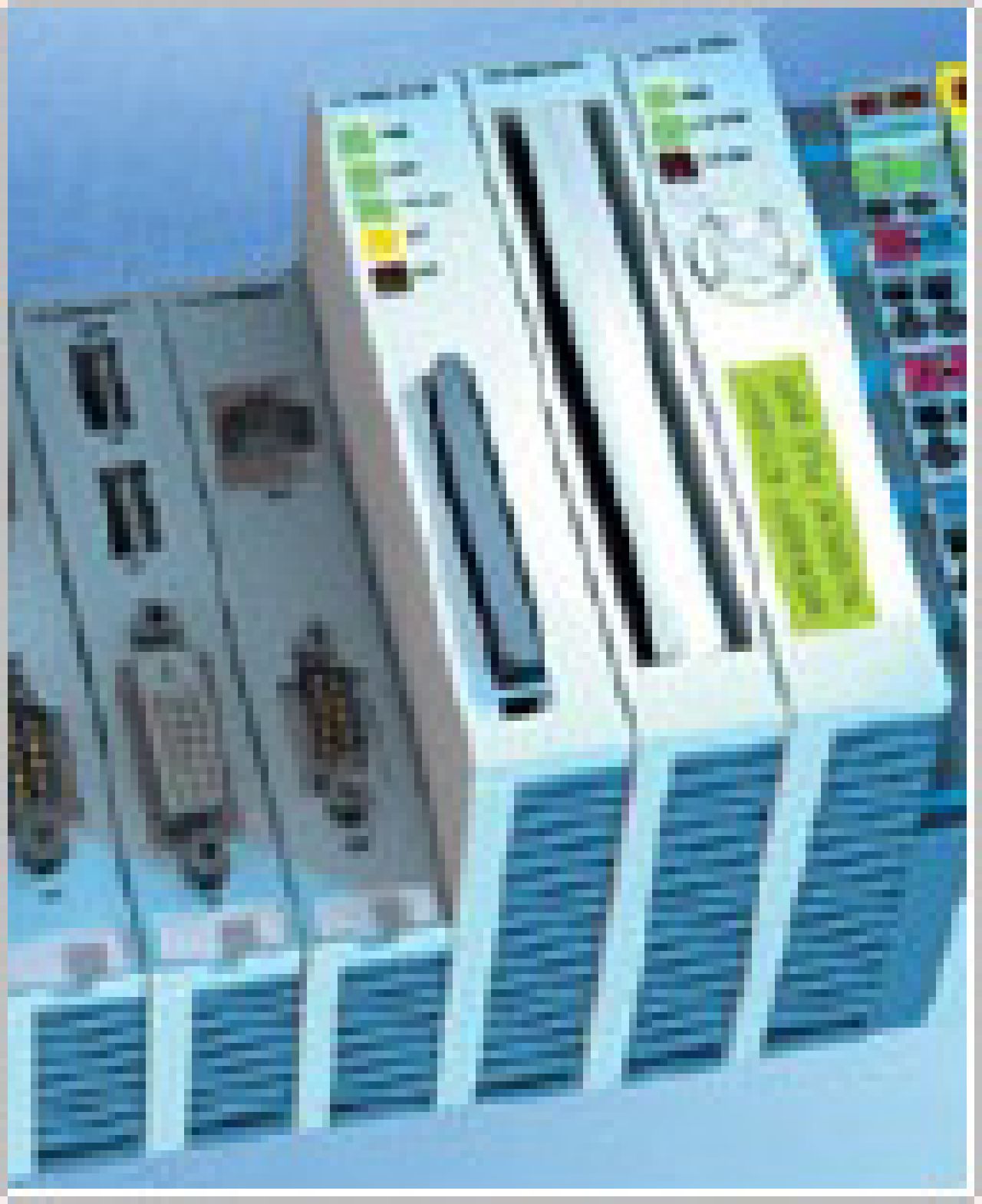
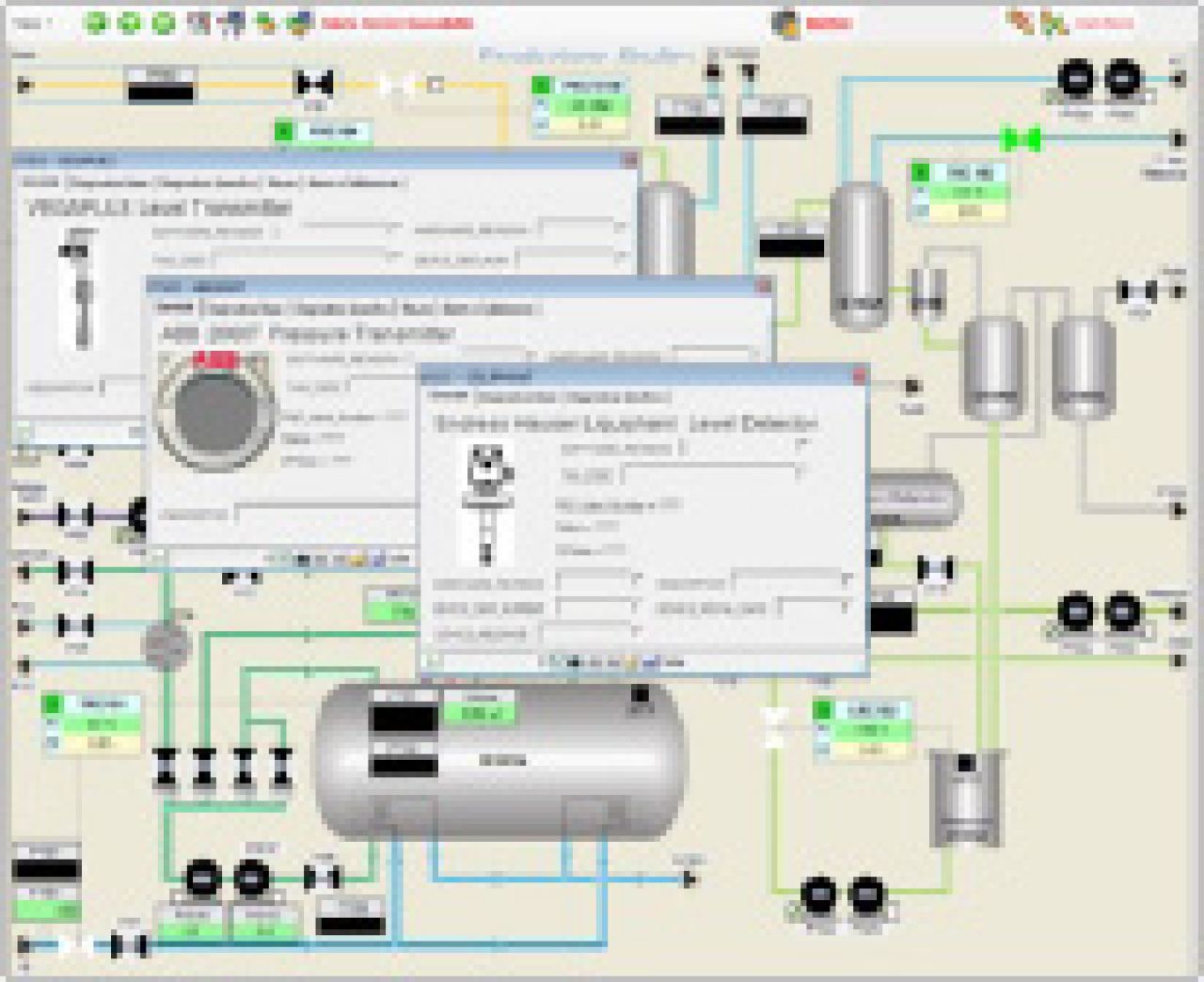
Il cliente
Il cliente, che si trova in Piemonte, produce diversi prodotti ottenuti con processi continui e batch. C.Si.Co. ha provveduto all’automazione di tutti gli impianti dello stabilimento (più di 20). In questa scheda si presenta la soluzione adottata per l’impianto di produzione di combustibile biodiesel.
Il progetto
Il cliente dispone, nello stabilimento, di infrastrutture idonee alla realizzazione del processo di produzione di biodiesel. Le problematiche principali sono legate al pericolo di esplosione, dovuto ai componenti in gioco, e alla estensione spaziale, poichè i serbatoi esistenti da utilizzare sono collocati su un’area estesa.
La soluzione
C.Si.Co. propone di utilizzare un sistema basato su periferia decentrata Profibus PA. Con questo standard europeo, tutta la strumentazione necessaria e l’acquisizione dei segnali dal campo risulta specificamente creata in conformità alle normative ATEX per le aree a pericolo esplosivo. Allo stesso tempo, Profibus PA consente di minimizzare i costi di installazione elettrica, poichè si basa sul trasporto di alimentazione e segnale sullo stesso supporto conduttore.
Ne risulta una riduzione drastica dei cablaggi, con risparmio in termini di materia prima (cavo), di costi di installazione (meno lavoro per elettricisti), di tempi di messa in servizio (test I/O) e, infine, di manutenzione, poichè la riduzione della complessità intrinseca porta con sè una riduzione del numero di guasti.
Per quanto riguarda il controllore, ci si orienta verso il PLC. C.Si.Co. ha sviluppato esperienze su molti dei sistemi più noti (Siemens S5, S7, PCS7, Allen Bradley, Omron, …), ma nel contempo impiega cospicue risorse nell’analisi delle proposte del mercato e propone quindi soluzioni alternative che, pur con performance non inferiori, hanno costi decisamente competitivi e consentono, per le caratteristiche d’avanguardia, di risparmiare nella realizzazione e manutenzione del software. Il cliente accoglie favorevolmente la proposta di C.Si.Co. ed in tal modo il controller scelto consente una riduzione dei costi di approvvigionamento hardware e sviluppo dell’applicazione software.
Per la supervisione, il cliente sceglie la soluzione C.Si.Co., basata su librerie e driver nativi per Windows.
Grazie a queste scelte, ed essendo tutta la strumentazione su rete, è possibile sviluppare sul controller e sulla supervisione gli strumenti per poter accedere alla configurazione e alla diagnostica degli strumenti in campo direttamente dall’applicazione di supervisione su Pc, con grande vantaggio per gli operatori e gli strumentisti e con costi hardware/software estremamente ridotti rispetto alle soluzioni tradizionali.
I risultati
Il sistema realizzato consente la produzione dell’impianto a ciclo continuo, con una capacità produttiva di centinaia di ton/giorno. In caso di guasto di uno strumento, la diagnostica integrata nell’applicazione consente di individuare immediatamente il problema. La procedura di sostituzione è altrettanto rapida, poichè dal punto di vista elettrico è sufficiente collegare il bus Profibus PA (2 fili), mentre la configurazione dello strumento viene scaricata in pochi secondi direttamente dal supervisore. L’installazione viene certificata secondo ATEX senza alcun problema. I controlli degli Enti preposti al controllo dei produttori di combustibile sono resi estremamente rapidi e semplificati dalla disponibilità realtime sul supervisore di tutti i dati necessari.
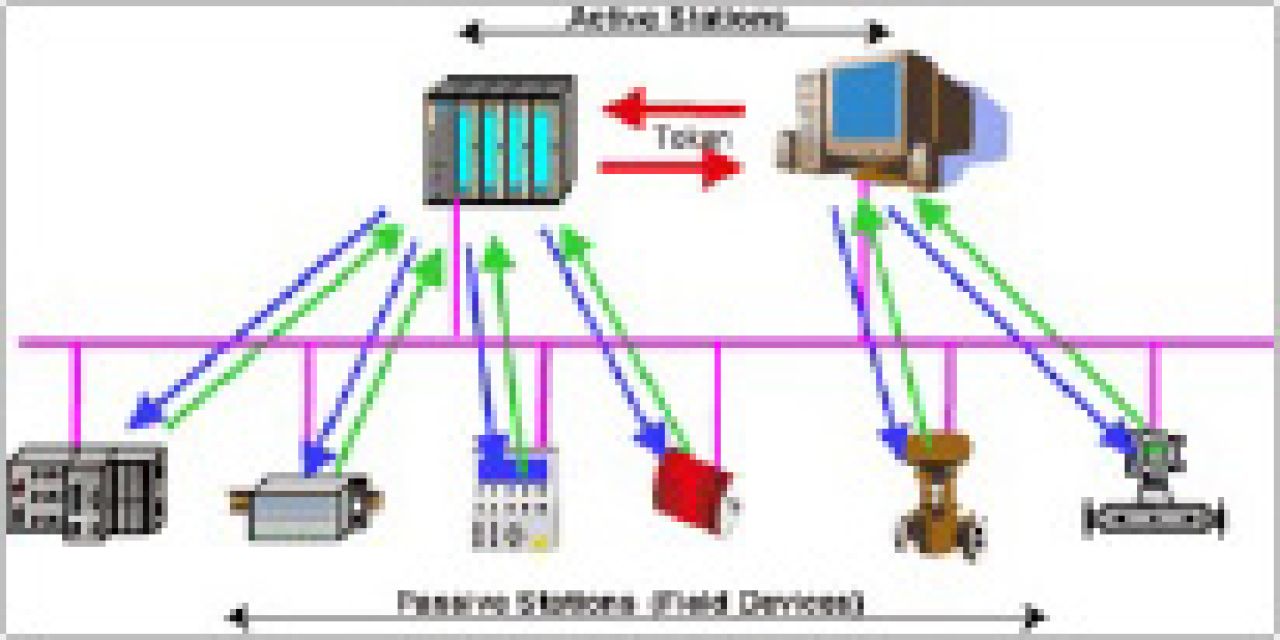
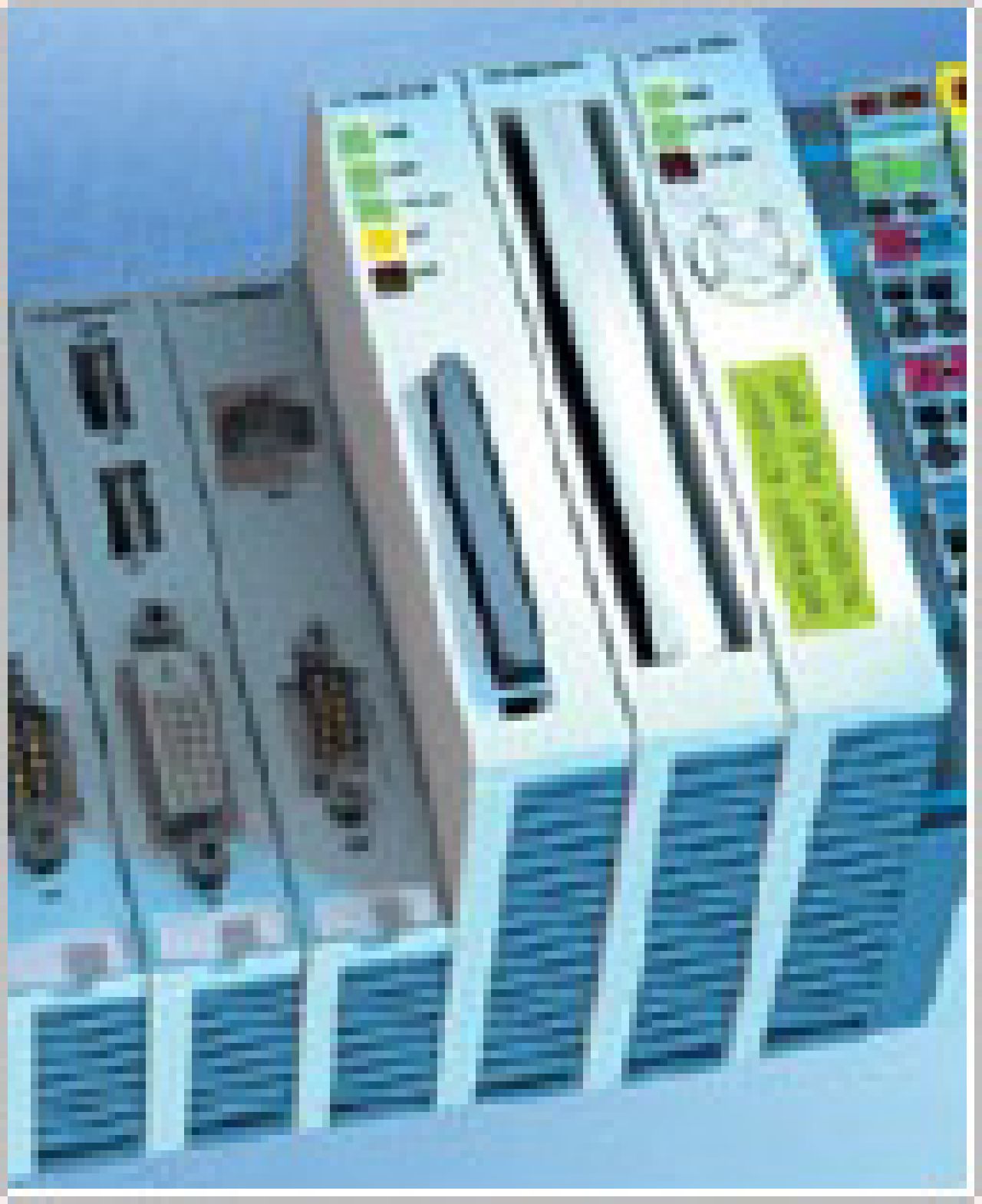
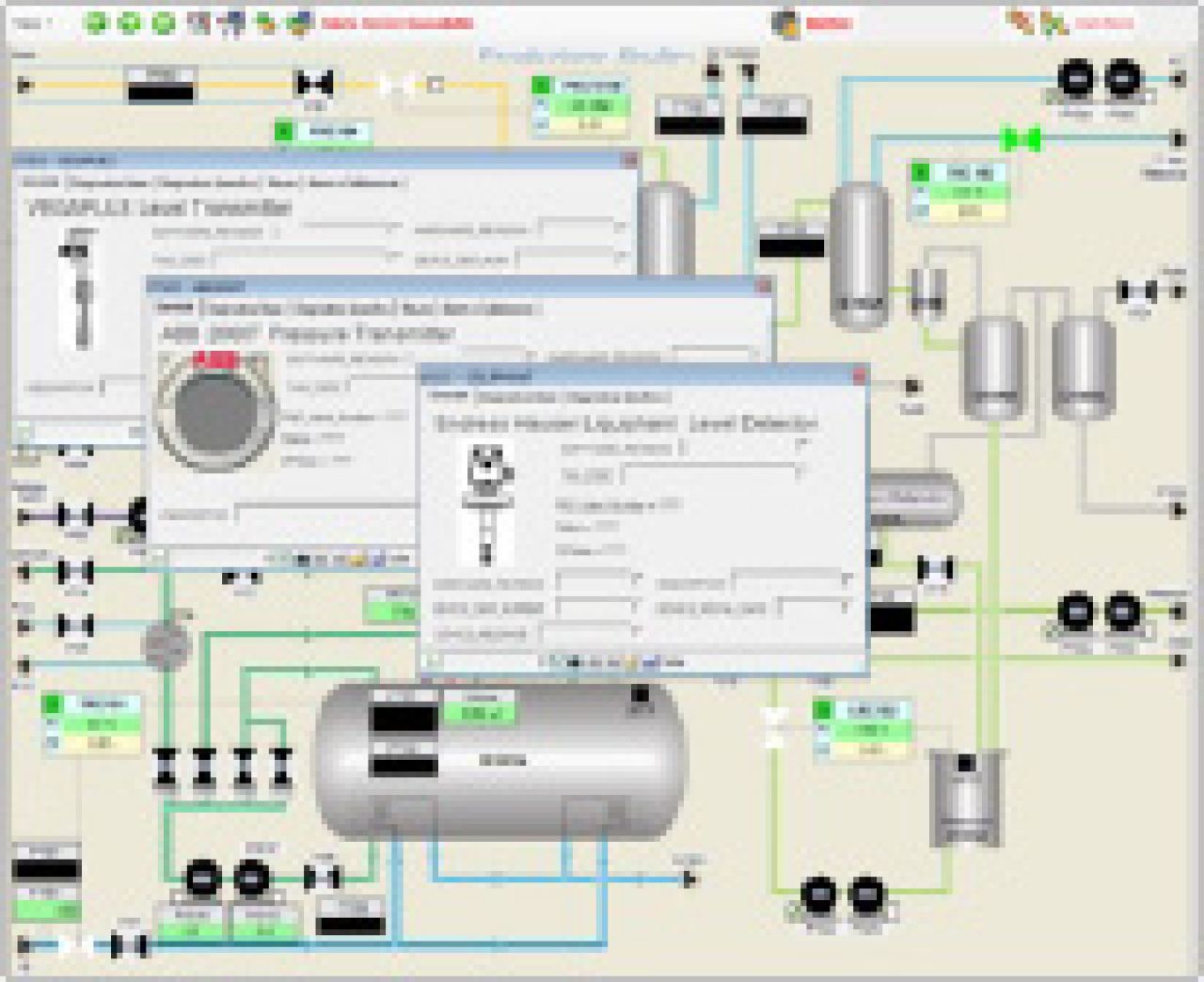