Caldaia industriale
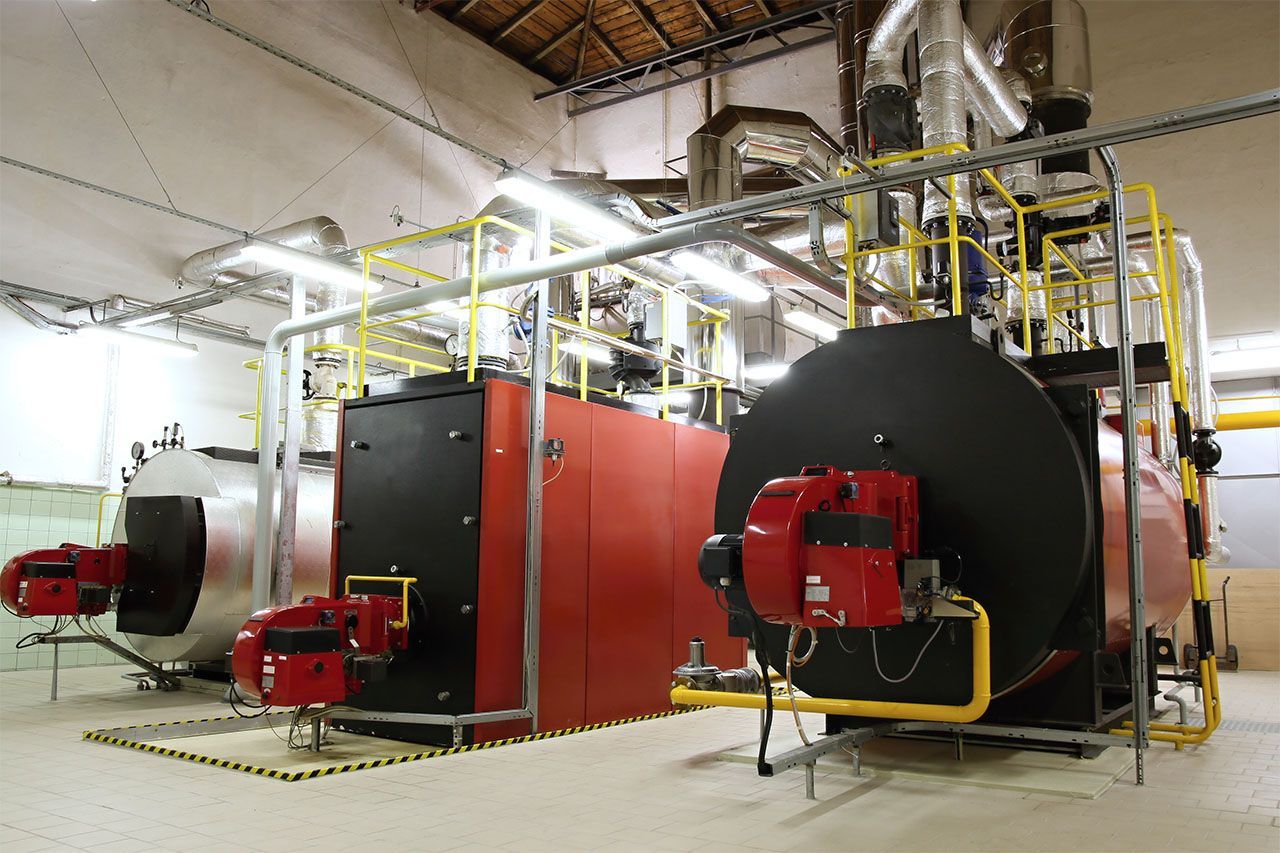
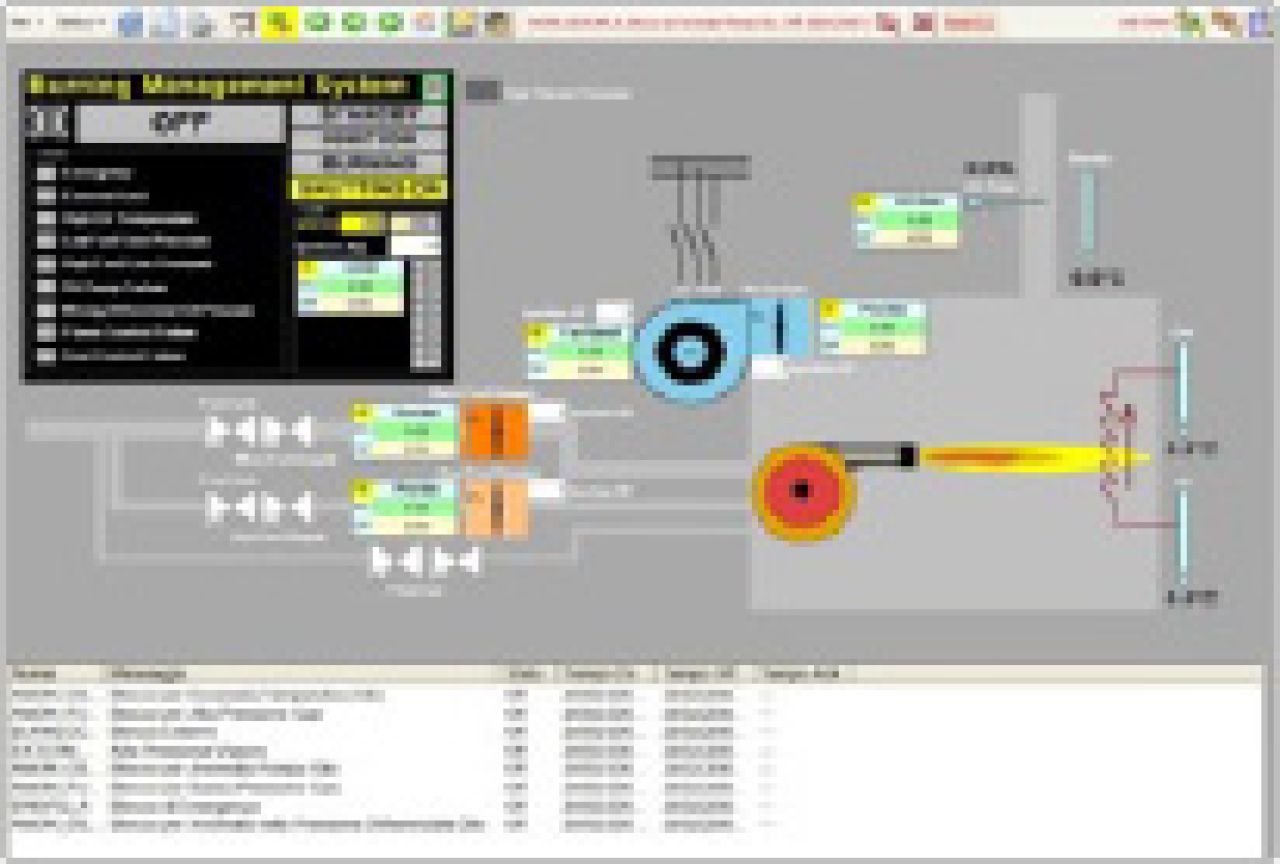
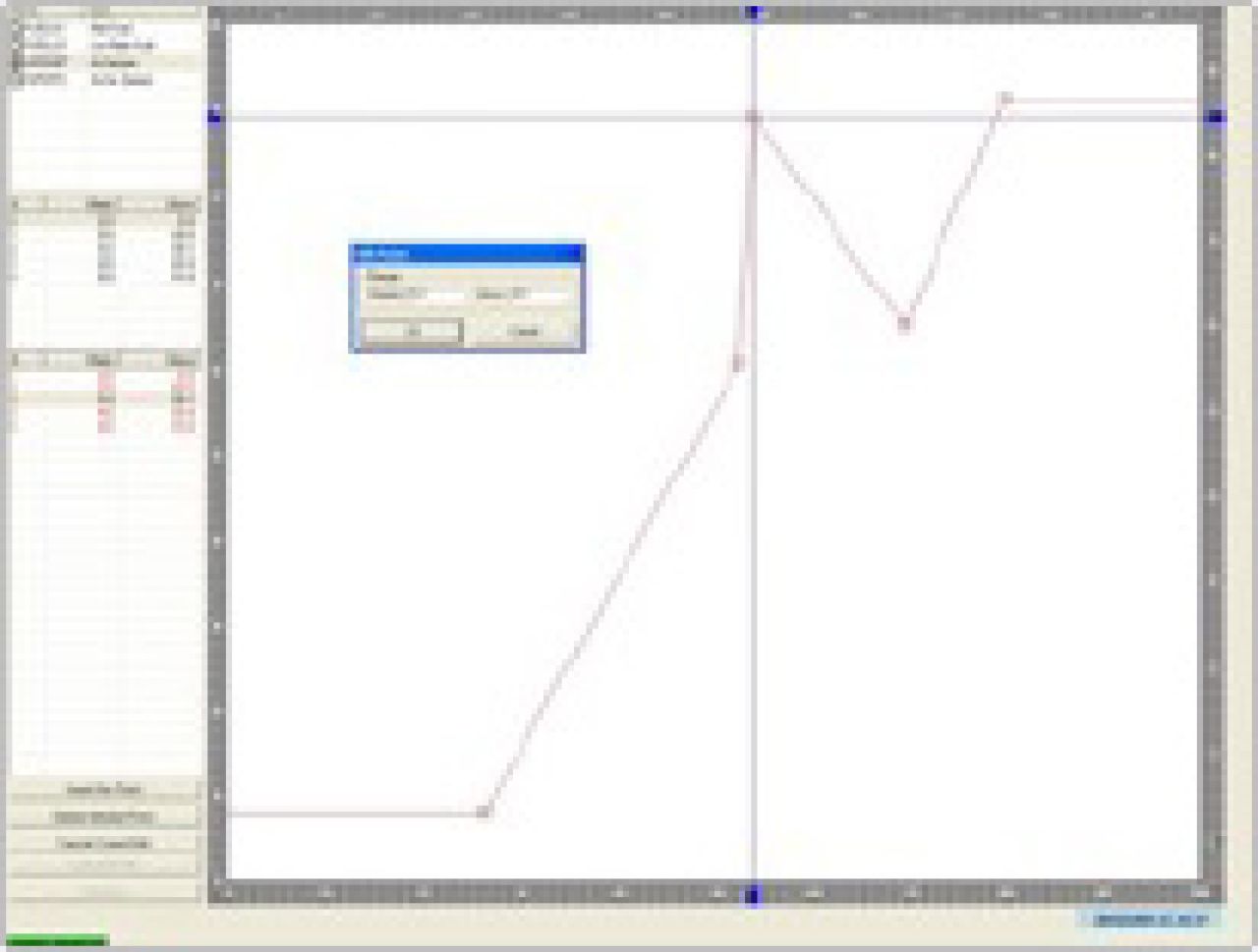
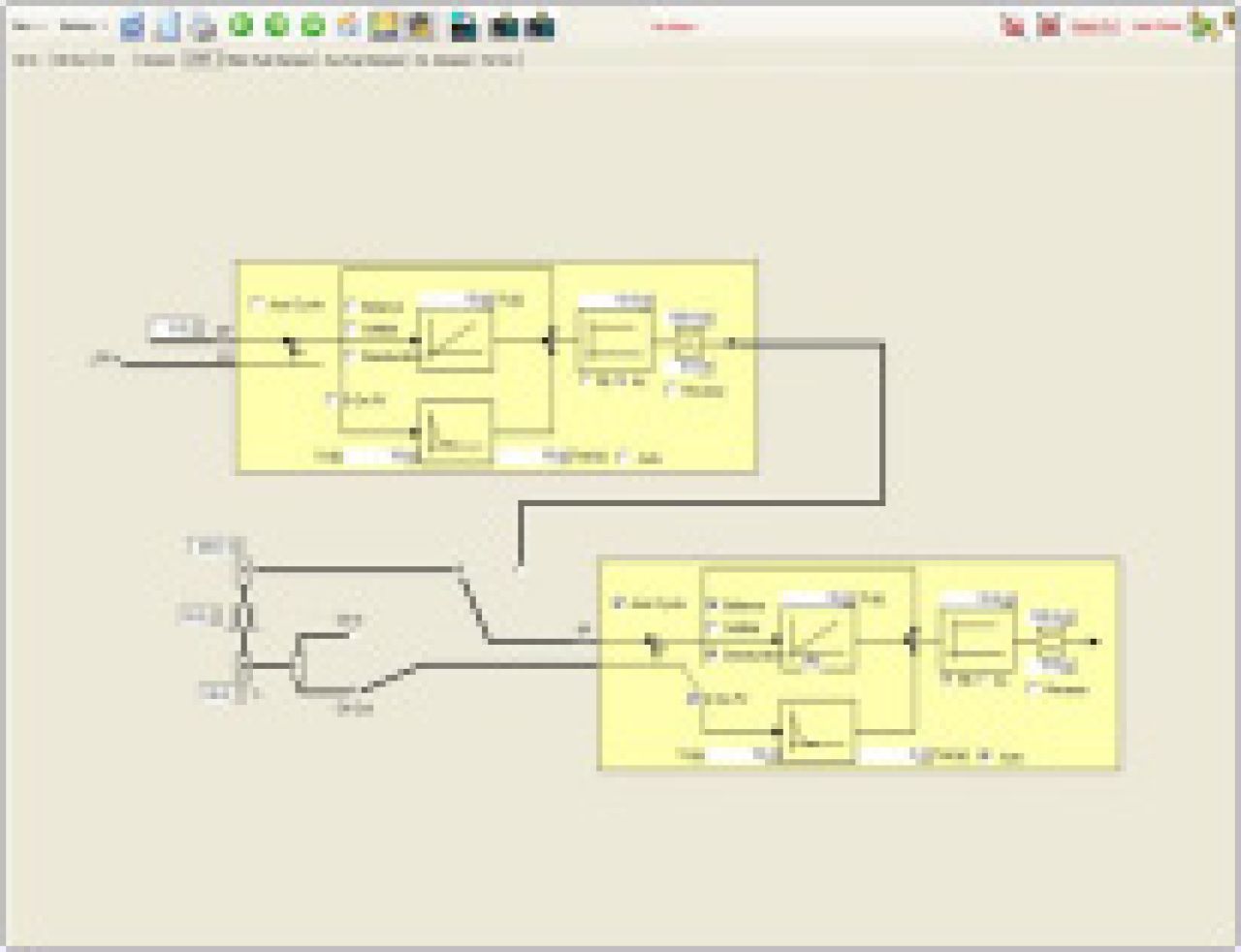
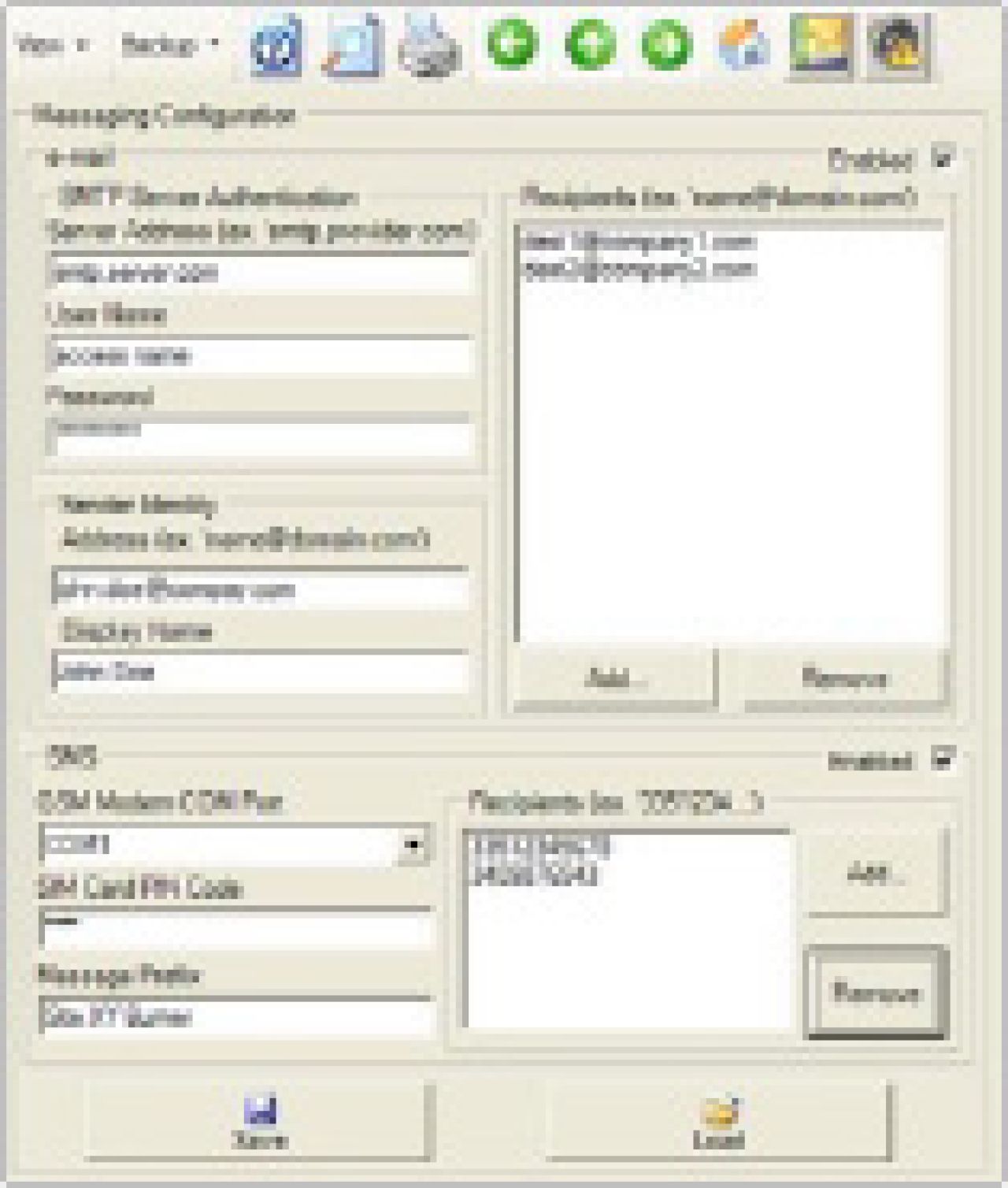
Il cliente
Il cliente, lombardo, è leader nella produzione di caldaie industriali.
Il progetto
Da tempo il cliente esplora la possibilità di dotare i suoi macchinari di un nuovo sistema di controllo automatico, che, rispetto all’attuale, consenta di raggiungere i seguenti obiettivi.
- Razionalizzazione: il sistema attuale è composto da diverse e variegate apparecchiature di mercato, ognuna necessaria per eseguire delle specifiche funzioni. In tal modo, nascono costi elevati dovuti da una parte alla sottoutilizzazione di ogni singolo modulo, e dall’altra alla realizzazione del necessario interfacciamento tra di essi.
- Funzionalità: con il sistema attuale, alcune funzionalità richieste dal mercato risultano di difficile o eccessivamente costosa realizzazione.
- Flessibilità e scalabilità: il cliente sente l’esigenza (un trend normale per il futuro), di spostare la realizzazione delle funzionalità dall’hardware al software. In tal modo, infatti, vi è più flessibilità nell’adattarsi alle esigenze specifiche dei clienti, nonchè la possibilità di abilitare o meno funzionalità del sistema senza necessità di intervento sull’hardware.
- Diagnostica e parametrizzazione remota: vi è la necessità di poter stabilire un collegamento remoto con il sistema di controllo, al fine di controllare la situazione diagnostica del sistema per eventuali interventi guidati a distanza, o per un tuning di parametri remoto, o ancora per monitorare le attività e le azioni degli operatori a fini di controllo.
- Analisi statistica: al fine di migliorare i prodotti, il cliente desidera poter raccogliere, sempre da collegamento remoto, dati storici relativi all’efficienza della combustione e alle emissioni, per poter effettuare una post-analisi sui dati raccolti.
- Interfaccia uomo/macchina: il sistema attuale consta di un pannello testuale per l’inserimento dei parametri, con una serie di pulsanti e led per le segnalazioni e l’operatività. Il cliente desidera che l’interfaccia sia più moderna, con qualità grafiche e user-friendly, più intuitiva sia per l’installatore che deve configurare i vari parametri, che per l’operatore che ha il compito di condurne l’esercizio.
La soluzione
C.Si.Co. propone la sostituzione di tutto il costoso hardware con un unico controllore.
Si tratta di una macchina scelta appositamente per soddisfare le esigenze del cliente. Il dispositivo proposto consente di realizzare, sulla stessa unità, sia le funzioni di controllo che quelle di interfaccia uomo/macchina.
Si tratta di un dispositivo industriale con sistema operativo Windows e runtime Soft-PLC, la cui validità C.Si.Co. ha già testato per diversi anni nelle sue installazioni.
La disponibilità del sistema operativo Windows, consente a C.Si.Co. di sfruttare a pieno le librerie e i driver creati per la supervisione, realizzando un applicativo personalizzato per questo caso, che, oltre alle normali funzionalità di supervisione, presenta anche le seguenti caratteristiche:
- Interfaccia grafica specifica per la configurazione delle curve di carico.
- Configurazione user-fiendly delle funzionalità.
- Funzionalità configurabile di messaggistica Sms e/o e-mail.
- Collegamento remoto per teleassistenza e supervisione remota.
I risultati
Il sistema così realizzato raggiunge tutti gli obiettivi di progetto, con un costo hardware inferiore a quello esistente di più del 65%. Considerato che il cliente vende un centinaio di macchine all’anno, il risparmio ottenuto è tale da compensare l’investimento nei primi 4 mesi di vendite. L’avere ottenuto un sistema più performante produce nel primo anno, un incremento degli ordini del 15%.
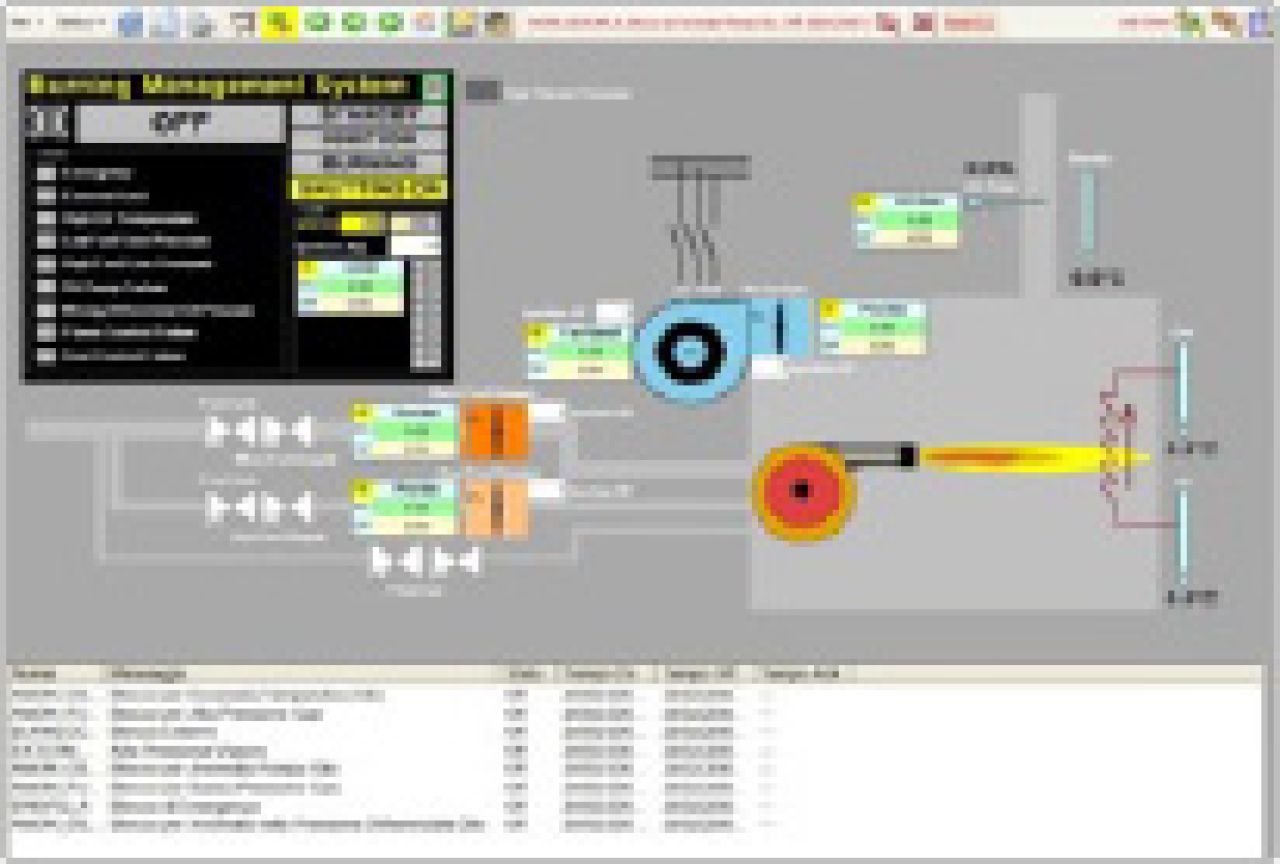
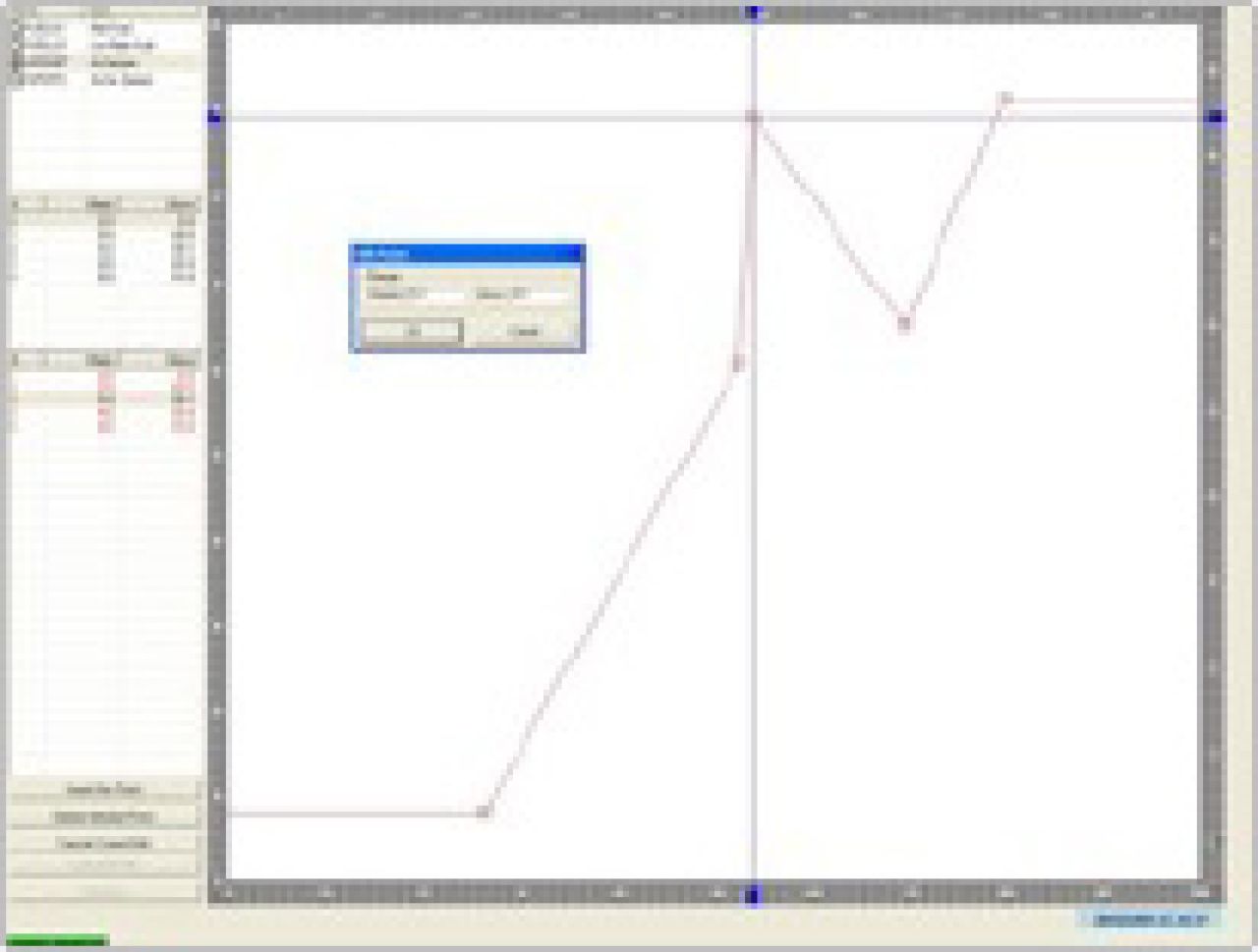
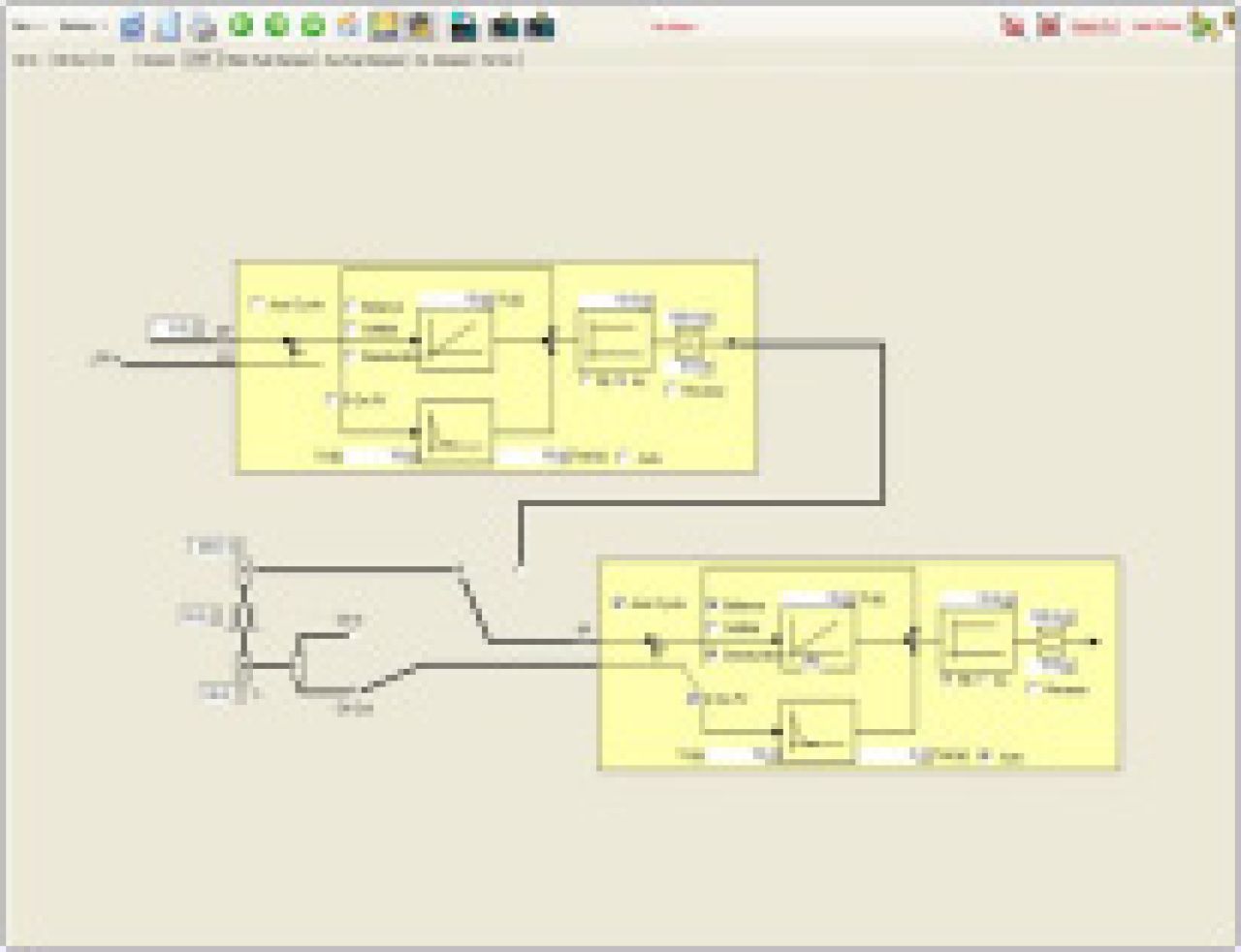
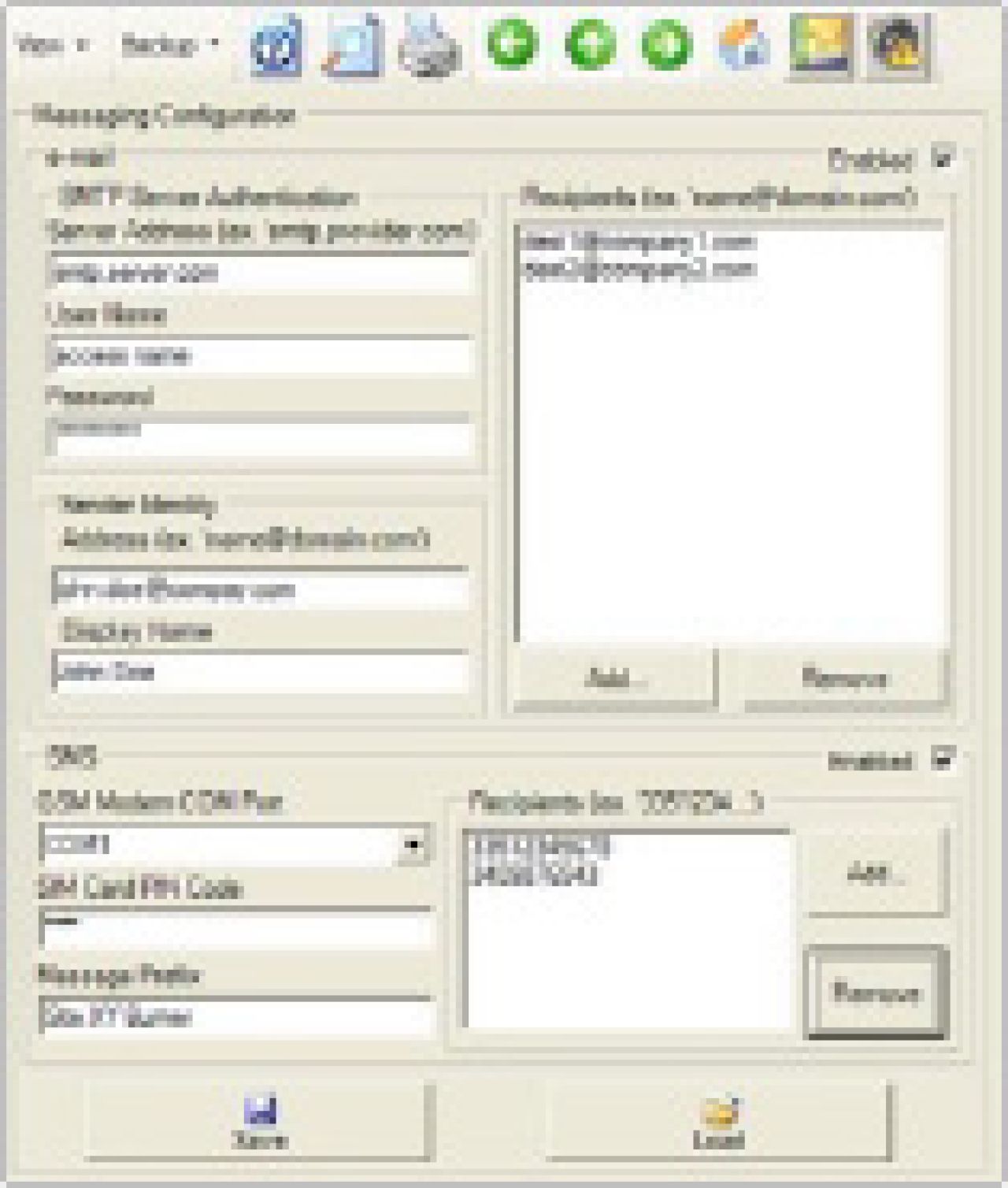